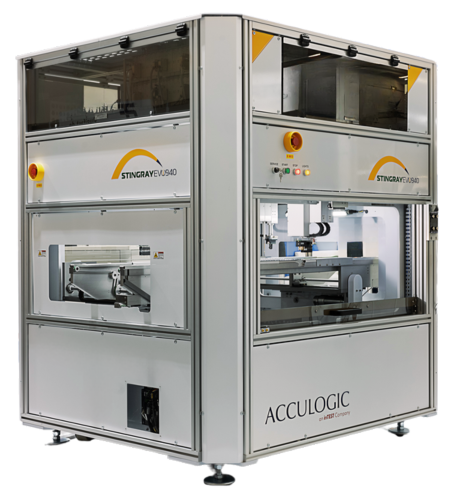
STINGRAY EVO500 Battery Tester
Quick, Reliable, and Cost-Effective Battery Module Interconnect Testing
Engineered for Performance
Highlights of the STINGRAY Battery Tester

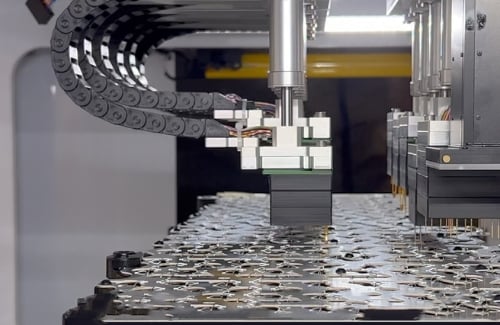
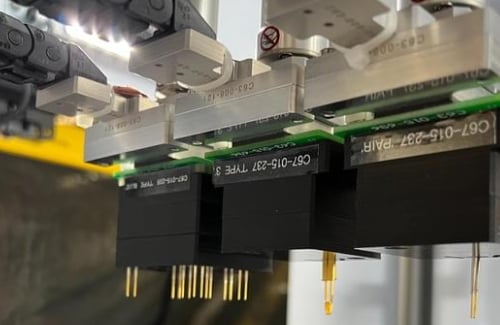
Every battery array that moves along the production line must be verified for the integrity of its interconnects. World-class manufacturers keep their production lines moving smoothly by investing in quality verification systems that quickly and reliably test the manufacturing quality of battery cell interconnects. By choosing the patented STINGRAY test platform, manufacturers gain a commanding advantage. The STINGRAY has repeatedly proven its value and technology with over ten years of production use and hundreds of thousands of battery arrays tested.
Poor quality cell interconnects can lead to several problems, such as increased resistance, leading to increased heat generation, voltage drop, and reduced overall performance. Also poor interconnects can also lead to safety hazards such as arcing, which can cause fires or explosions.
Battery cell interconnect issues must be caught during battery production. Otherwise, field failures can be costly and harmful to a company’s reputation. For battery manufacturers, it is critical to have a production test solution that can quickly, reliably, and cost-effectively test battery module interconnects.
Configurable modules for performing necessary tests
Flying Multi-Pin Probe Module | Thermoscan Probe Module | Hover Sense non-contact | Laser Scan | Camera |
![]() |
![]() |
![]() |
![]() |
![]() |
A Superior Solution for Battery Test
Having 1 STINGRAY is like having dozens of hardworking, unerring, untiring test technicians committed to thoroughly testing all your battery modules for on-time shipment.
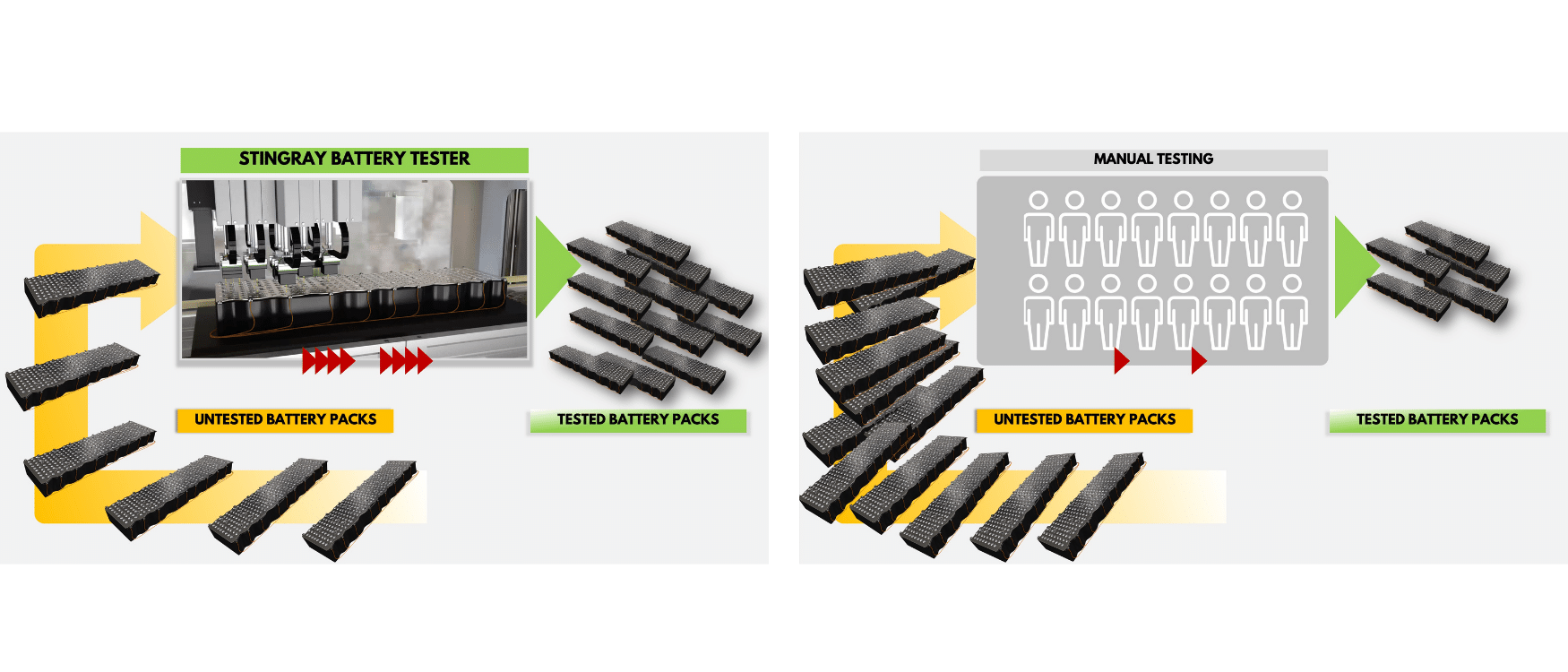
Patented, Industry-Leading Technology
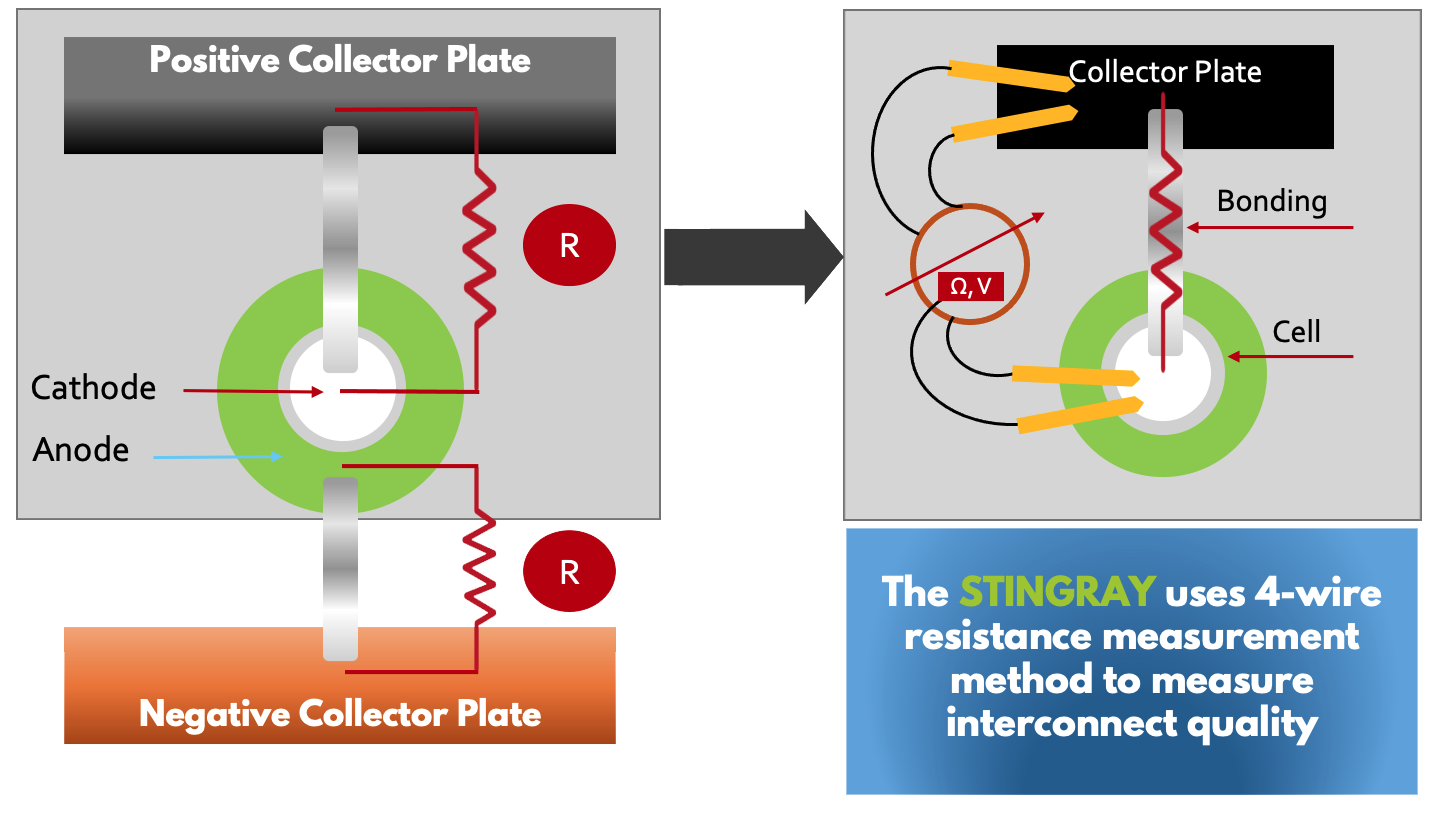
Measurement Methodology Ensures Accuracy, Reliability & Repeatability
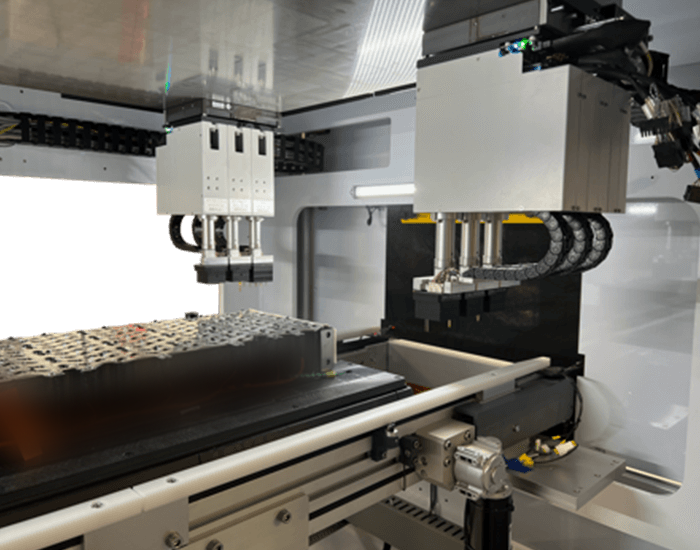
Independent Robotic Positioning System delivers maximum
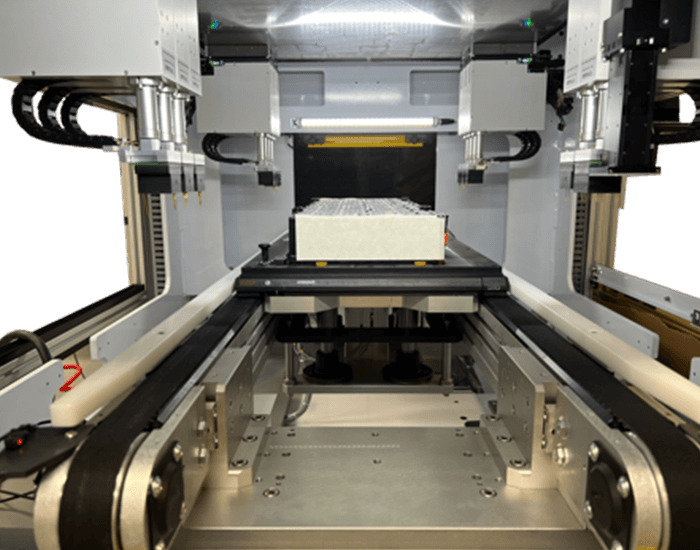
Maximizes battery testing throughput by:
Benefits of the Stingray Automated Battery Test Solution
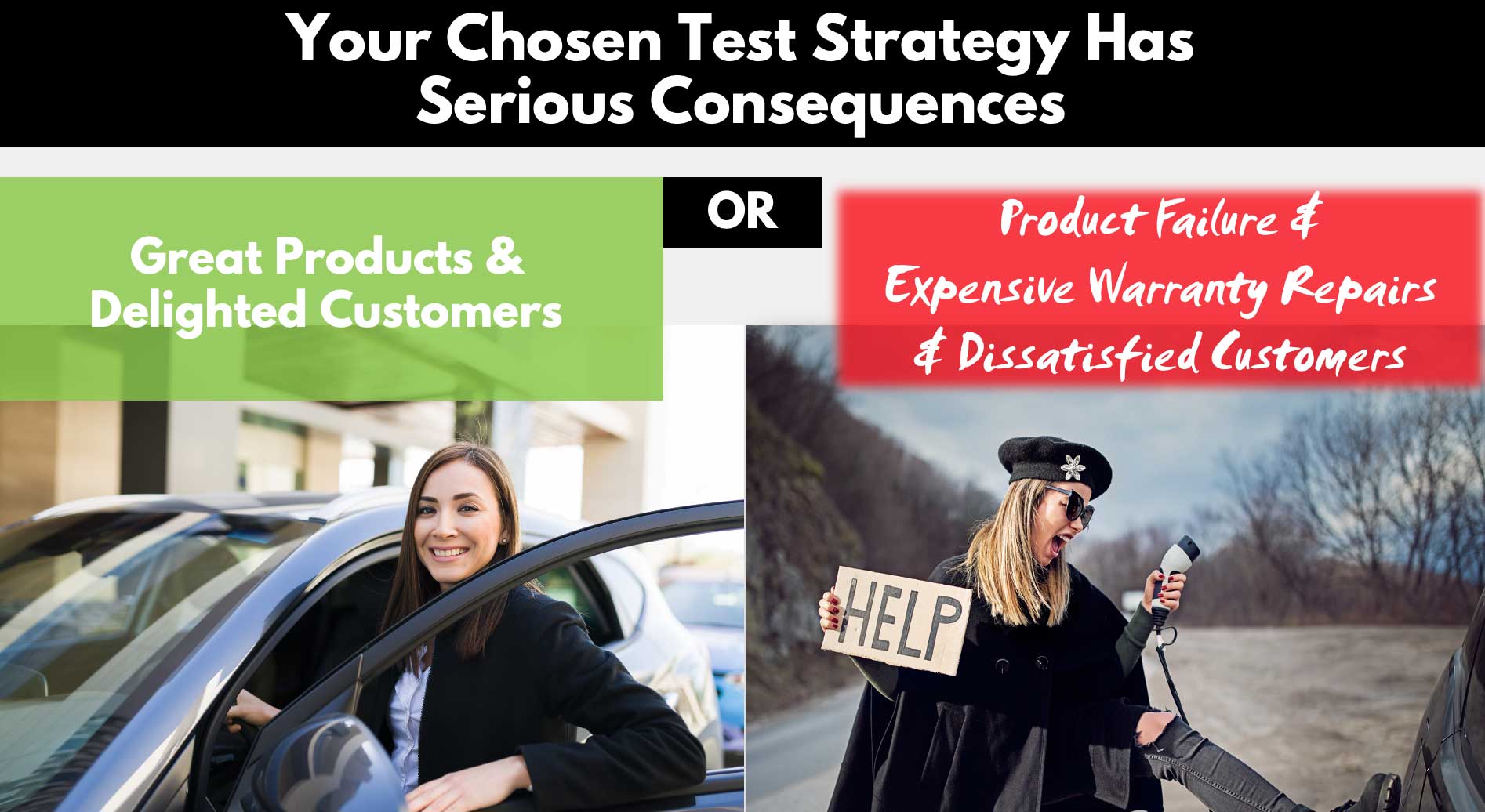